Machining centers are the backbone of many production lines. Ultra-precise, fast, and versatile, they make it possible to manufacture complex parts with high-quality standards. But in today’s competitive landscape, it’s no longer enough for a machining center to simply run—it has to perform efficiently and consistently.
The good news is: there are many ways to optimize performance—especially by leveraging the right data.
Machining centers: a major investment
A modern machining center represents a significant investment. According to Machines Production and Industry Week:
- A standard 3-axis CNC machining center starts around €100,000
- High-end 5-axis machines range from €300,000 to €600,000
- Specialized or automated machines can exceed €1 million, not including tooling and maintenance
On top of that, operating costs remain high—energy, consumables, wear, and unplanned downtime all take their toll.
That’s why maximizing every hour of machine uptime is essential.
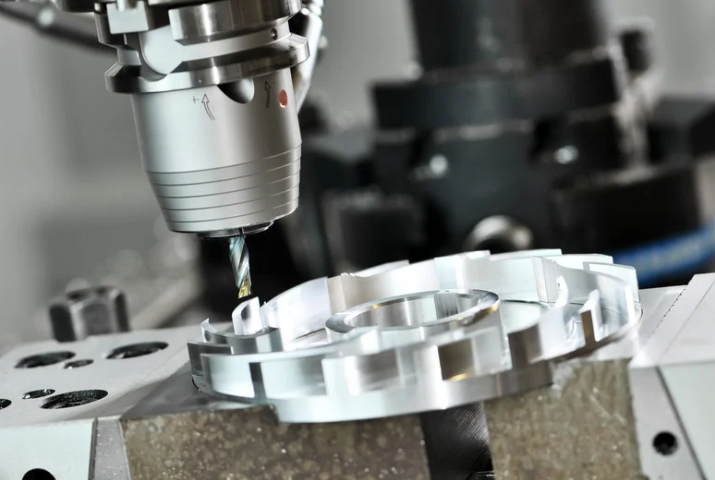
The true cost of a machining center breakdown
According to the Predictive Maintenance Market Report 2023, each hour of downtime costs between €3,000 and €22,000, depending on the industry. For a machining center—especially one integrated into an automated line—costs can be even higher.
And it’s not just lost output. Downtime also leads to:
- Scrapped parts and quality issues
- Requalification and inspection delays
- Team disruptions
- Possible delivery penalties or customer complaints
Bottom line: a minor defect can quickly become a costly chain reaction.
The limits of traditional maintenance
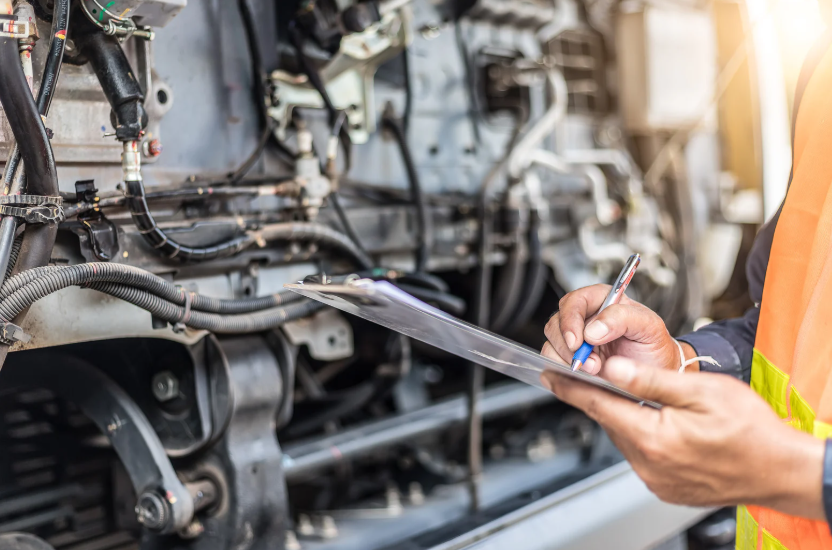
Many workshops still rely on preventive maintenance based on the calendar. But here’s the problem: that doesn’t reflect the machine’s actual condition.
Some parts get replaced too early. Others fail unexpectedly.
A Capgemini study revealed that nearly 50% of maintenance managers find their current strategy inefficient
What the market says: data is king
The global CNC machining center market was valued at $83 billion in 2023, and it’s projected to hit $128 billion by 2028 (Markets & Markets). Growth is being driven by:
- The rise of Industry 4.0
- Increased traceability and quality control requirements
- The need to produce faster, with fewer defects
In this context, data collection and analysis have become essential tools.
Collect the right data, at the right time
With a solution like Lesly, you can connect your machining centers to:
- Monitor machine status in real-time
- Detect and analyze micro-stops and causes
- Accurately calculate OEE (Overall Equipment Effectiveness)
- Spot behavioral drifts using AI
- Estimate the remaining useful life of key components
Lesly leverages data from CN, PLC, Drive, and IoT, even across multiple machine brands. And all of this happens without needing a complex infrastructure—or a data scientist.
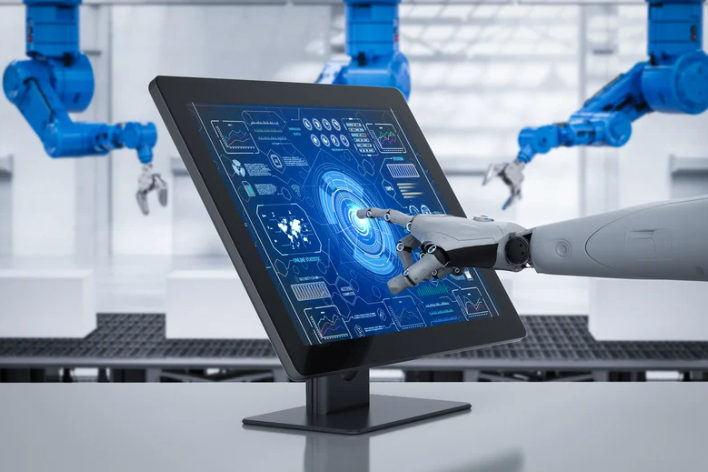
Real results on the shop floor
With a data-driven approach, measurable gains follow quickly:
- +30% longer component lifespan
- -20% scrap rate
- +40% machine availability
- Smoother team operations
- Less stress from last-minute breakdowns
Best of all: ROI is visible within the first few months.
Fast deployment, zero friction
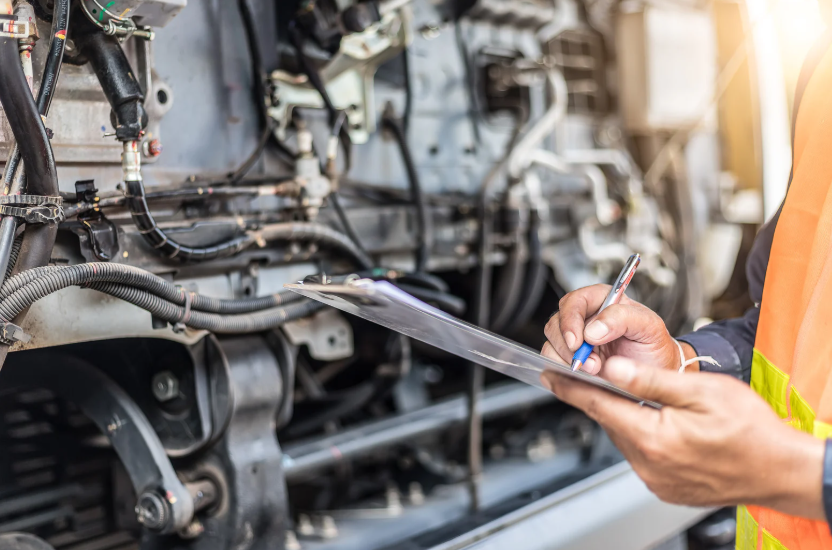
Lesly installs across your machining centers using a single software on an industrial PC for centralized monitoring. In most cases, full deployment takes less than 4 weeks, including:
- Machine criticality analysis
- Connection and parameter setup
- Reference data collection
- Team training
You keep your current machines and processes. Lesly simply adds a layer of industrial intelligence.
Conclusion: performance comes from insight
Optimizing a machining center isn’t just about faster cycles. It’s about producing better, more consistently, with fewer surprises. With intelligent data collection and real-time analysis, every minute becomes a chance to improve.
With Lesly, you’re not reacting to machine issues anymore—you’re leading the performance.
Contact us for a free consultation and personalized quote