Technological advances are transforming the manufacturing industry. Among the major innovations, data analysis plays a central role in the management of industrial machinery. Big data can be used to optimize performance, reduce costs and prevent breakdowns, improving productivity and competitiveness. This article explores how data analysis is revolutionizing industrial equipment management.
1. Data analysis in Industry 4.0
The concept of Industry 4.0 is based on the integration of digital technologies into industrial processes, thanks in particular to the Internet of Industrial Things (IIoT) and cybersecurity systems. Connected machines collect data in real time, enabling us to better understand how they work and identify inefficiencies. This process, known as predictive analysis, transforms equipment management into a precision science.
Concrete example of data analysis :
Imagine a car production plant. Sensors installed on the machines continuously detect information on temperature, vibration and production speed. This data is then analyzed to anticipate a failure before it occurs, thus avoiding costly downtime.
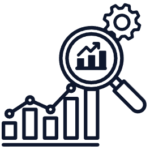
2. Predictive maintenance: Reduce breakdowns and optimize productivity
Traditionally, the maintenance of industrial machines has been carried out either on a preventive (planned) or corrective (after a breakdown) basis. Thanks to data analysis, a third, more efficient method has emerged : predictive maintenance.
How does it work?
Machine learning algorithms analyze the data collected by the sensors to identify patterns and anomalies indicating a potential breakdown. This enables maintenance managers to take preventive action before the machine breaks down, reducing downtime and extending equipment life.
Benefits of predictive maintenance :
- Reduced maintenance costs: Fewer breakdowns mean fewer costly repairs.
- Increased machine life: By anticipating problems, critical components are replaced in good time, extending equipment life.
- Optimized productivity: Unplanned downtime is reduced, improving continuity of operations and reducing production losses.
3. Optimizing machine performance
Data analysis goes beyond simple maintenance. It can also be used tooptimize the performanceof industrial machines. By analyzing historical and real-time data, it is possible to adjust machine parameters so that they operate at maximum efficiency.
Case studies
In a food production line, data analysis can be used to adjust conveyor speeds and oven temperatures to obtain the optimum end product while reducing energy consumption.
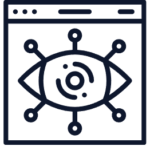
4. Improving processes with artificial intelligence (AI)
Artificial intelligence and machine learning make data analysis even more powerful. These technologies, combined with industrial data, open up new perspectives for improving manufacturing processes.
AI-enabled systems can learn from past data to propose adjustments in real time. For example, a machine can automatically adjust its parameters according to fluctuations in demand or the state of raw materials. This increases flexibility and improves the quality of finished products.
5. Lower energy costs
Energy optimization is a priority for many industries. Data analysis makes it possible to monitor and optimize the energy consumption of machines. Analysis systems identify when a machine is using too much energy, and adjust its operation to reduce consumption.
Example
In a chemical plant, sensors monitor the energy consumption of reactors in real time. By cross-referencing this information with production requirements, the system can adjust machine power to minimize consumption while maintaining product quality.
Contact us for a free consultation and personalized quote
Conclusion
Data analysis is revolutionizing the management of industrial machinery, offering new solutions for optimizing maintenance, improving performance and reducing costs. Thanks to technologies such as the Internet of Industrial Things (IIoT), artificial intelligence and predictive maintenance, companies can now take advantage of real-time data to better manage their machines and stay competitive. Digital transformation is underway, and data analysis is one of the key drivers in the industrial sector.